Lesson 1 Drill Presses
Drill Presses and Their Use
Student Pre-reading
Word List
1.) button | a small round piece which sticks out; when pressed it is an ON/OFF switch. e.g., Jorge, when you want to turn off the machine, press that button. |
2.) computer | an electronic machine which stores information and uses it to do complex operations. e.g. Chung Li got a new computer for Christmas. |
3.) to concentrate | to study one thing very carefully and not to worry about other things. e.g., In this lesson we will concentrate on kinds of drill presses. |
4.) downward | in a down direction away from up. e.g., Sid moved the handle downward, and the drill moved down toward the workpiece. |
5.) to elevate | to lift up, to raise up. e.g., This screw is able to elevate the heavy radial arm, because it is big and strong. |
6.) latest kind | the newest model of some product. e.g., Manny always buys the latest kind of sports car. |
7.) much larger | bigger by much more. e.g., A radial drill is much larger than a sensitive drill. |
8.) project (noun) | a special piece of work that has its own goals and deadlines. e.g., My project for the next month is to investigate and buy a new computer for myself. |
9.) radial | ![]() branching out from a center like a ray of light from the sun. |
9.) right away | immediately, without delay. e.g., My wife is having a baby; she needs to go to the hospital right away. |
10.) sensitive | able to feel easily and well. e.g., His hands are very sensitive to heat and cold. |
11.) spare parts | extra parts; parts made for later use. e.g., The Boeing Aircraft Company always makes spare parts for its planes. |
12.) stationary | not moving, fixed. e.g., The milling machine table moves during the cutting; the drill press table is stationary.root word: stay |
13.) stop | a device used to stop the motion of some other part. e.g., The drill press has a depth stop to prevent the drill from cutting too deeply. |
14.) to tilt | to cause to slope or slant. e.g., The table can be tilted in order to drill a hole at an angle. |
Spelling
Matching Definitions
DRILL PRESSES AND THEIR USE
In this last module you will complete your study of large machine tools. You have already learned about lathes and milling machines. Now you will study drilling machines and grinders. In this lesson you will concentrate on drill presses.
1. Main Kinds of Drill Presses: All drill presses have some features in common: First, they all have a stationary table which holds the workpiece securely. Second, they all have a rotating spindle which holds the cutting tools and which feeds in a downward direction into the work. This feed can be manual or automatic. The main purpose of any drilling machine is to make accurate holes in a workpiece.
Learn the main types of drill presses:
a. Sensitive drill presses: These are drill presses of smaller size; some models sit on top of a workbench and are bolted to it; others stand alone on the floor of the shop. They are called “sensitive” because the machinist is able to feel and see how well the drill is cutting into the material and can make changes in operations if they are needed.
b. The upright drilling machine: This drill press is like the sensitive drill press, except it is bigger and stronger. It will always stand alone on the floor. It usually has a greater variety of controls for both the spindle and the table.
c. The radial drill press: The main feature on this machine (which the other two types do not have) is the radial arm on which the drilling head and the spindle are mounted. This arm allows much larger pieces of work to be drilled. With the arm, the drilling head can be moved quickly to any location on a big workpiece. Additionally, this machine has more power than the other two kinds and can use larger cutting tools to make bigger holes.
As you look at our two pictures of a sensitive drill and a radial drill, you should know that the radial drill is a much larger machine than the sensitive drill, though it might not appear that way in the picture.
d. Numerical control drill presses: These are the latest kind of drills; they are controlled by a punched paper tape or by a computer; they are good for doing repetitive, very accurate operations, over and over.
2. The Main Parts of a Drill Press and the Purpose of Each: Let’s look first at a sensitive drill press. It is important to learn the name and purpose of each part on a drill press.
a. Table: This holds the workpiece securely. Some tables are rectangular, others are round. They can be raised, lowered, swiveled around the column, and, sometimes, they can be tilted to drill a hole at an angle. The table surface usually has T slots for clamping a vise or a fixture, or for clamping the workpiece directly.
For taller workpieces, the table can be swiveled out of the way, and the work can be secured directly to slots cut in the base.
b. Drilling head: This part contains the mechanism which rotates the spindle. The spindle holds and rotates the cutting tool; the spindle is located inside a metal sleeve called the quill; the quill does not turn, but it slides up and down inside the drilling head to allow for feed into the work.
c. Controls: A hand feed lever with one, two, or three lever handles is used to feed the drillbit down into the work. Some machines are equipped with automatic feed. The machine also has a depth stop which can be set to stop the downward advance of the drill at a certain depth of cut, and not to go too deep. There are other controls, like the buttons for ON and OFF and the speed control to choose the desired RPM setting.
d. Other parts: The radial arm, on a radial drill press is attached to a heavy column and is raised or lowered by a power-driven elevating screw. On the radial machine, the drilling head can be moved to any position along the arm; the head slides on a set of ways cut into the sides of the arm. The rates of feed and speed are controlled by mechanisms in the drilling head.
Let’s practice what we just learned.
Fill in the Blanks
Matching
Parts Identification
Matching Names
Spelling with missing letters
Identification
Student Conversation Sheet
First, listen to the tape marked ”Mod 9, Les l “, and practice the parts. Then find a partner and practice with that person.
Situation: Paul is talking with Bill.
Paul: I’m a little confused, Bill. I see these different kinds of drill presses, and I’m not sure which one to use for my project.
Bill: The reason we have different kinds is because each one is good for doing a certain kind of job. Tell me more about your project. The» we can decide which to use.
Paul: Well, I only need to make six of this part; it’s here in the blueprint. Two parts will be used right away, and the other four will be kept as spare parts.
Bill: With a small order like that, it wouldn’t be practical to set up a numerical control tape–that’s for when we need hundreds or thousands.
Paul: Perhaps the size is what will help us decide what machine to use.
Bill: Very good idea! The size of a machine is measured from the center of the spindle to the column of the machine. The largest machine is the radial drill. The radial arm allows it to drill very large pieces.
Paul: Well, my project isn’t that big, but I think it’s going to take a larger drill than that little one mounted on the workbench.
Bill: That little one is a sensitive drill–it’s used for lots of jobs, but if you want something bigger, then I suggest the upright drill; it’s good for medium size work, and it’s also more powerful than the sensitive drill.
Accessory Names
Matching Names
Spelling with missing letters
Accessories Identification
DRILL PRESS ACCESSORIES
The drill press uses several accessories to help drill accurate holes. Some are for holding tools; others are for holding the work.
1. Tool-Holding Accessories:
a. Drill chucks: A drill chuck usually has three jaws that tightly hold the straight shank of a drillbit or other cutting tool. The jaws are tightened by the use of a chuck key. The pilot of the key fits into the hole in the chuck, and the teeth on the key mesh with the teeth on the sleeve of the chuck. When the key is turned, the three jaws tighten around the shank of the drill bit.
The chuck itself is mounted in the spindle by a tapered end or by a threaded end.
b. Drill sleeves: This accessory is used to adapt the size of a small drill bit to a large drill. At one end, the taper of the drill sleeve will fit into the large taper of the spindle on a large machine; at the other end, the drill sleeve has a smaller tapered hole into which the smaller drill bit will fit.
c. Drill sockets: This accessory does the opposite of the drill sleeve by adapting a large drill bit to the small taper of the spindle on a small machine. The drill socket also acts as an extension for giving greater length to the drill bit.
d. Drill drift: This tool is used to loosen tapered accessories or taper-shanked tools from the spindle where they are usually very tightly fit. The drill drift is inserted and tapped with a hammer.
2. Work-Holding Accessories:
a. Drill clamps: These clamps are held in place by T-bolts inserted into the T-slots of the drill press table. In this picture the work is held by a drill clamp; the short end of the clamp is holding the work and the long end is resting on a table block of equal height.
b. Drill vises: There are several kinds of vises which will attach to the drilling table; the drill in the picture will hold a variety of different kinds of stock: round, rectangular, and odd-shaped pieces. There are other vises which will hold the work at an angle in order to make holes at an angle to the surface of the work.
c. V -blocks: A good way to hold round work is in a set of V-blocks. They have V-shaped grooves into which round work will fit; clamps will hold the work tightly in the blocks. They are made of steel and usually come in pairs.
There are many other accessories for the drill press which you will learn when you go to the machine shop. These are some important ones. They will be of great help to you when drilling holes.
Comprehension Check
Accessory Identification
DRILL PRESS OPERATIONS
Using different cutting tools, the drill press is capable of doing a variety of operations. The more common ones are listed here:
1. Drilling: This operation makes holes in material by the rotation of a cutting tool called a twist drill. The hole is cut by the cutting edges (cutting lips) at the end of the drill and by the cutting edges along the sides of the drill. The twist drill has three main parts: the shank, the body, and the point.
a. Shank: The shank can be tapered (when the drill diameter is 1/2 in. or greater) or straight (dia.= less than 1/2 in.); the tapered shank will have a flat end (the tang) which keeps the drill from slipping in the drill spindle.
b. Body: This is the part between the shank and the point. It has two or more grooves (the flutes) cut into its sides. These flutes have sharp edges to help with the cutting; they also provide clearance for the chips to escape and for cutting fluid to run into the drilled hole.
c. Point: The twist drill cuts with its end (the point) which has several parts: the cutting edges (called the cutting lips), the chisel end (at the very end of the point), and the heel. The angle of the point can be varied to suit the hardness of the material being drilled.
The twist drill should be kept sharp for greatest efficiency. Twist drills will last longer, when they are sharp, and when the machinist is careful to follow the charts for correct feed and speed for the material being drilled and for the material used to make the drill.
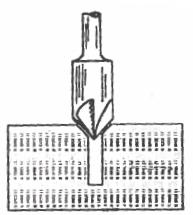
2. Countersinking: A countersink cutting tool is used to make a cone-shaped, larger hole at the end of a hole that was previously drilled. This allows a screw head to drop below the surface of an assembled part.
3. Counterboring: A counterbore cutting tool is used to make a larger straight hole at the end of a hole that was previously drilled. This gives a shoulder and a space into which a bolt head can fit and be below the surface of an assembled part.
The counterbore has a pilot end to guide the tool into the original hole.
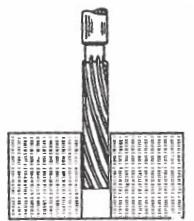
4. Reaming: The reamer has a cutting edge down its sides; it is used when the machinist wants to produce a very accurate, very smooth, perfectly round hole. The reamer is run into a previously drilled hole; it removes small amounts to make very exact dimensions inside the hole.
5. Tapping: The tap drill is a special cutting tool used on the drill press; it is inserted into a hole which has been previously drilled with a twist drill. The machinist uses the tap drill when he/she wants to cut internal threads on the inside of a hole, so that a screw or bolt can be inserted. The sides of the tap drill have cutting teeth which will cut the threads. The tap drills come in a variety of sizes to make threads of various dimensions. In an earlier lesson (Module 3, Lesson 5) we saw that tapping can be done with a set of hand taps, as well as by machine.
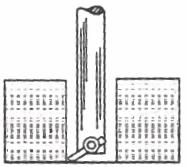
6. Boring: The boring bar is a tool which holds a single-point cutting tool for use inside a previously drilled hole. The cutting tool will enlarge the hole and make the dimensions more exact. The drill press is less often used for boring than are special boring machines or the vertical milling machine, but boring can also be done on the drill press.
Matching
Spelling
Matching
Spelling
Idenification